成本直降40%,效率提升300%——無需百萬投入,2D視覺技術正重塑中小工廠品控邏輯
青島某電子元件廠曾面臨這樣的困境:每月300萬顆微型接插件需人工目檢,20名質檢員三班倒仍無法攔截0.3mm的引腳偏移。直到一批出口訂單因細微缺陷遭客戶索賠,損失高達季度利潤的15%。
這樣的場景在中小制造企業中絕非個例。當人力成本攀升與質量要求嚴苛形成雙重擠壓,輕量化、快部署的2D視覺識別系統正成為破局關鍵。
01 中小企業質檢困局:每道傷痕都是利潤的流失
在金屬加工車間,反光表面掩蓋的劃痕難以辨識;在注塑產線,透明材料內的氣泡逃過人眼捕捉;在裝配工位,錯漏裝問題常在交付后才暴露...這些看似微小的缺陷,正在不斷蠶食企業生存空間:
更嚴峻的是,某包裝廠老板坦言:“90后質檢員離職率高達80%,崗位招聘周期比設備安裝還長。”
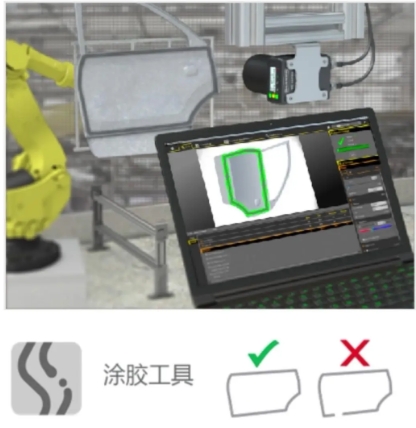
02 技術破壁:2D視覺的工業級進化
現代2D視覺系統通過光學革新與智能算法的融合,在成本可控前提下實現精密檢測:
成像技術突破
算法能力躍升
青島某緊固件廠的實踐顯示:部署2D視覺后單件檢測時間從3秒壓縮至0.5秒,月度質量成本下降37%。
03 實戰案例:可復制的成功范式
案例1:電子元件智能全檢
某接插件制造商部署在線檢測系統:
系統直接對接MES生成質量云圖,使工藝缺陷定位效率提升10倍。
案例2:包裝印刷品控革命
某食品包裝企業采用移動式檢測臺:
實時監控色差ΔE<1.5、文字漏印、套印偏差
檢出0.3mm²的污點與劃痕
免產線改造設計,當日部署即投產
年避免客戶索賠超180萬元,新客戶驗廠通過率提升至100%。
案例3:沖壓件在線分揀
汽車配件廠改造現有產線:
0.8秒內完成孔位定位(±0.02mm)、毛刺識別、外形尺寸檢測
機械手自動剔除不良品
系統自學習功能適應模具磨損變化
使產品報廢率下降52%,人均產出提升3倍。
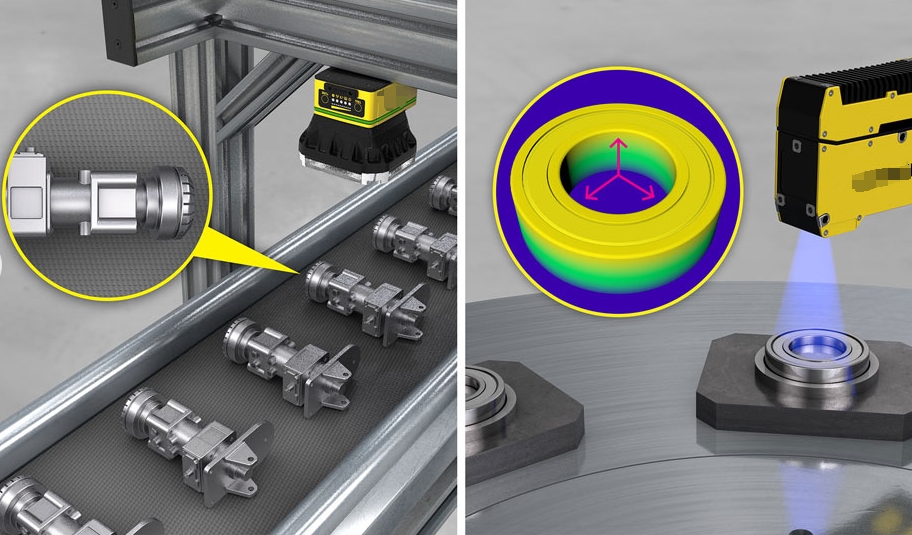
04 落地路徑:三步實現零風險轉型
針對中小企業痛點設計的漸進式方案:
階段 | 實施重點 | 價值錨點
▶ 試點突破 → 選擇返工率TOP2工位 → 單點ROI<6個月
▶ 數據積累 → 建立缺陷特征數據庫 → 定位核心工藝缺陷
▶ 系統融合 → 對接PLC/MES系統 → 實現質量閉環控制
青島某鈑金企業僅投入12萬元啟動關鍵工位檢測,6周后因質量索賠減少收回成本,二期自然擴展至全產線。
當浙江某閥門廠憑借2D視覺系統實現全年零客戶退貨時,生產總監在晨會上宣布:“這套系統不是成本支出,而是我們最好的利潤創造者。”
在工業檢測領域,精度與成本的平衡藝術正在被重新定義。青島的制造企業們發現:那些曾屬于行業巨頭的技術紅利,如今通過輕量化2D視覺方案,正轉化為中小企業觸手可及的核心競爭力。
【技術貼士】
新一代邊緣計算視覺系統支持:
✓ 斷電續檢:意外中斷后自動接續檢測
✓ 自診斷功能:實時監控相機/光源狀態
✓ 免代碼配置:圖形化界面實現檢測流程搭建
工業級2D視覺外觀檢測:精密、高效、易部署的智能質檢方案